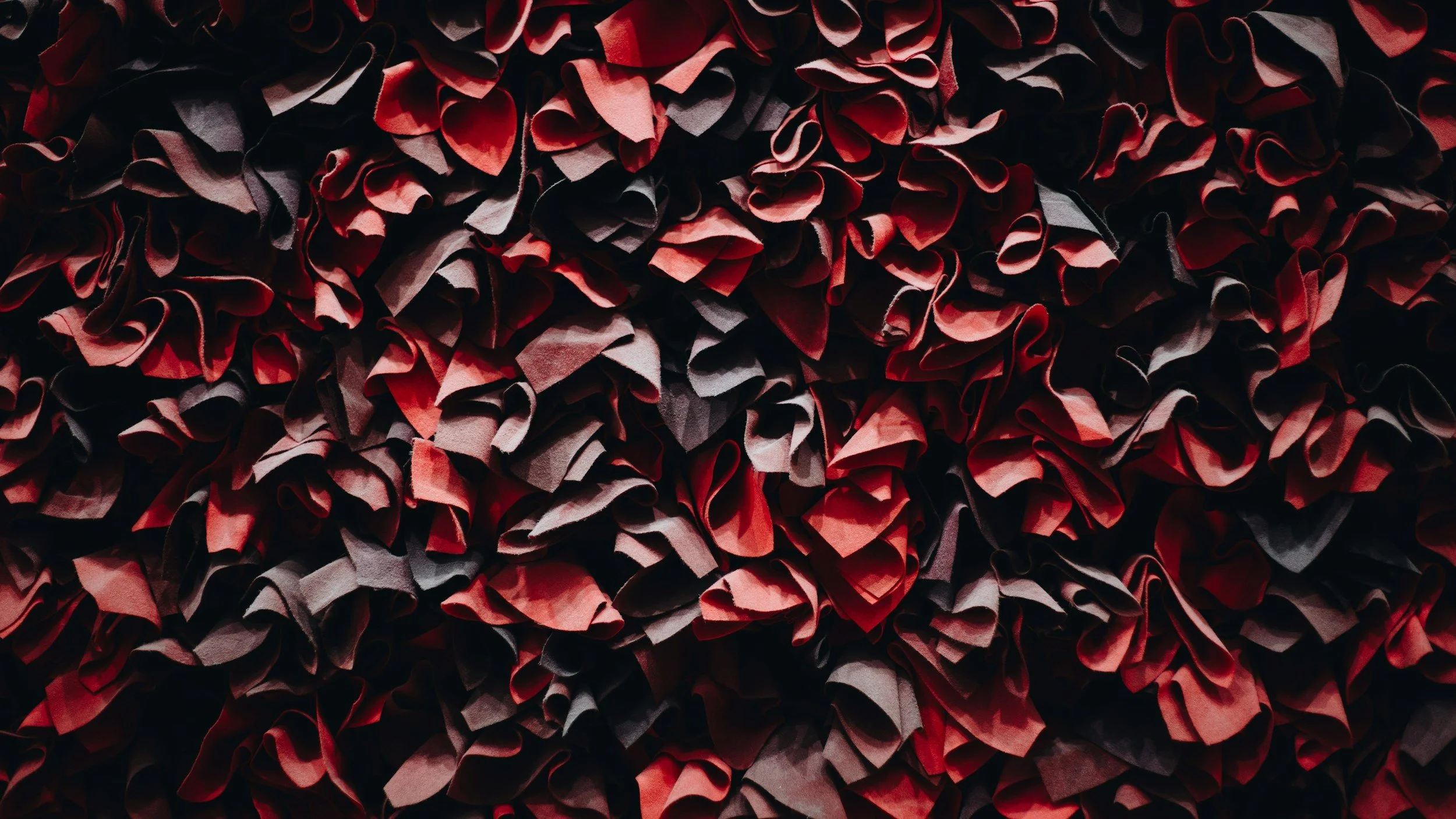
It makes all the difference.
Our Materials
Leather:
First of all, I don’t use synthetic, vegan, faux, or “genuine” leather on anything, ever. Beyond that, I use vegetable tanned leather on the vast majority of pieces. There are a few pieces I have made that used chrome-tanned leather, and this decision was made based on the function of that item. Furthermore, I often will select a different leather for different parts of one product, weighing practicality with style— texture, color, weight, balance, contrast. More information on tannage and a glossary of these leather terms can be found here.
Most importantly, I want to do more than just make a leather accessory that will last 20 years. I want it to look good.
Other Materials:
Many, many other materials are used in the process of creating a leather good. However, there are key components that enhance the user experience of our products. With hand-stitched products, thread choice is incredibly important. To retain the earthy “leather smell,” choice of adhesive really matters. The blend of waxes coating a burnished edge can impact the longevity of a piece. Combine all these things (and more) together, and you get a substantially higher quality product. All of these factors have been extensively tested over the years and refined to a perfect balance.
Over time, I would love to share details of the trial-and-error I have had with these nitty-gritty details with my clients and other craftsmen alike. Leather is an integral part of daily human life and woven intricately through thousands of years of human history worldwide. Many parts of this landscape have changed in the industrial revolution, and information on quality craftsmanship and materials are not nearly as accessible to consumers.
If you’re interested in trying your hand at leatherwork or exploring what others use in their craft, I would be happy to share what I have learned or just talk shop- scroll all the way down to the bottom of this page for contact information.
Hardware:
I could talk all day about leather but when it comes to hardware, there is a serious risk I’ll never stop. Every item has a different purpose, and therefore requires different qualities of its hardware, excluding the particulars of style.
This is how I approach the issue of hardware. With belts, it may be a casual, everyday belt picking up a lot of wear and tear but a staple in the user’s wardrobe. Durability and longevity are key, so I use solid brass with no plating. A “fashion” belt, however, is a belt made to pair with a particular outfit or color scheme in semi-regular circulation, and it’s all about the look. This is where I might use a plated buckle, and I always opt for PVD as it yields a thicker plating. Additionally, this is why I use Chicago screws instead of rivets. They are much stronger than most rivets and allow for less intrusive repair; if plating wears through on a belt, I can replace the buckle and touch up the edges of the strap.
Then, the dress belt. When you have an important interview , a business trip, or a hot date— what are you wearing? Belts, like shoes, can make or break a look. Mooney Leather Goods offers a selection of beautifully finished stainless steel hardware. The perfect, refined combination of satin finishes and high polish gives elegance and style to a look without being too flashy.
Not everything is about the leather— Mooney Leather Goods’ commitment to quality encompasses every aspect of the final product, from leather, to thread, to glue, and of course hardware.
Conceria Walpier
One of 19 tanneries in the prestigious Pelle Vegetale Consortium preserving traditional vegetable tanning techniques, Conceria Walpier has been producing top grade, robust, and vibrant hides for over 50 years. There are three specific articles of Walpier that we use quite often at Mooney Leather Goods: Buttero, Burro, and Rocky.
Buttero is their top grade leather and may be the ideal leather: vegetable-tanned, fully aniline, retaining the natural features of the hide with a subtle, elegant luster that will develop and deepen over time. On the firmer side, this lends perfectly to “every day” accessories such as a belt or wallet exterior and with Walpier’s vivid, classic range of colors it is guaranteed to stand out. I use Buttero in various weights on a wide range of products from belts, wallets, keychains, and even ring stands. Pictured on the left is a bundle of straps of both Rocky and Buttero, the two primarily used in our belts. Rocky is slightly firmer, but very similar to Buttero.
Burro is my absolute favorite leather. It is made with a Buttero hide finished with a layer of white wax that picks up scratches easily to reveal the vibrant color beneath. In the meantime, the wax shines up beautifully with minimal friction either intentionally with a cloth or just from contact with denim pockets or handling. Burro adds dimension and personality to any piece, as well as strengthening the bond between the user and the item.
Mégisserie Alran
Nestled in the heart of the Black Mountains, Alran has long been a staple in the shoemaking industry and in the 1980’s expanded their legacy to the fashion industry. A leading specialist in fine chevre leathers, Alran leathers can be found in pieces by some of the biggest designer brands in the world. Alran is known best for their unique hand boarding process, bringing texture and depth across their extensive color palette. Their Sully hides in particular are a favorite at Mooney Leather Goods for its iconic, luxury feel— most often used as a bag liner or wallet interior.
Badalassi Carlo
Another member of the Pelle Vegetale Consortium, Badalassi Carlo is known for producing some of the highest quality vachetta leathers in the world, used worldwide in shoemaking, high end bags, and small goods. If you’re interested in luxury brands, their vachetta Box leather will look awfully familiar. We’ve taken a particular interest in their Pueblo leathers (pictured right, color Sapphire) for their truly unique rustic look. I am not generally a fan of “rustic” aesthetics, but Pueblo is rustic done right. The surface is scratched lightly in small circles to reveal the bright, vivid color just below the grain surface and as this detail changes with wear, the full aniline finish deepens to highlight the natural features of the hide. The patina developed over time is truly unique, and from a tannery specializing in soft, luxurious feeling, you can count on the experience of this leather enhancing with age.
Horween Leather
Finally, Chicago’s own Horween Leather. Founded in 1905 and for a meaningful stretch the leather supplier of the United States Army, the go-to shoemaking leather for a vast array of celebrities and US presidents for over 100 years, and the manufacturer of the leather used in the NFL game ball each year.
While there is a revived interest in their world renowned Shell Cordovan, especially being implemented outside of shoe-making, that’s not exactly the direction Mooney Leather would like to go. Horween leather makes a beautiful boot, but is kind of difficult to burnish, difficult to skive, and just not ideal for small items like wallets though many of their leathers are vegetable tanned. I like to use their Dublin leathers for a more casual belt.
Because they supply leather to the sports industry, occasionally we are able to get our hands on their football or basketball leathers (pictured right), which make for interesting and fun textures, as well as a nod to a classic Chicago company.
Conceria La Bretagna
A family-owned and operated Tuscan tannery specializing in traditional vegetable tanning (yet another member of the prestigious Pelle Vegetale Consortium), their Gaucho Oil and Pecos leathers certainly stand out in the array used at Mooney Leather Goods. Like many other tanneries in the MLG lineup, they are known again for their colorful range, but with Pecos it is a slightly more pastel selection and with a slightly matte top grain lending beautiful contrast to a wallet interior (pictured left, color Pistachio). Alternatively, their Gaucho Oil features a glazed finish— used often as an exterior in our minimalist bifolds wallets. Both of these finishes are a full aniline finish- La Bretagna masterfully achieves truly striking textures without concealing the natural features of the hide. It is a celebration of the medium and the place we hold in nature.
But what about design and craftsmanship?
It is important. Craftsmanship and design skills are key for selecting hardware and leather because you have to know what you can do with them and what you want to do with them. Our process is slow and meticulous and of course, carried out entirely by hand.
The Process
-
I may start with an idea based on function, like a sunglasses case for example. I think about what the product needs to do (protect and carry sunglasses), what I want to avoid (floppy design that risks the glasses being crushed, scratchy interior), then I sketch 1-5 functional ways to construct the piece. Then I choose the best or sometimes best two, and start sketching the whole piece from various angles to narrow down the aesthetics. Maybe I want to add flair with a weird stitch or a unique flap shape on the closure. Finally I annotate potential color combinations or specific hardware I would like to use.
-
Now I start to play with leather. I decide what weight makes sense for this piece because as leather is bent, different weights will require completely different dimensions. I also decide what the “base system” is- for wallets, everything is based around the dimensions of American currency and/or standard business cards. For a bag, I want everything to assemble very precisely because one error becomes exaggerated in such a large piece, so I use the length of a stitching chisel as the base measurement in the design. All of this is laid out on graph paper and a prototype is made to see how it really feels, looks, and performs.
-
When I have made an acceptable prototype, the dimensions described in my notes are then measured out to scale on plastic pattern sheeting and cut out. Thanks to Chuck Dorsett from Weaver Leather Supply, every hole to be punched is circled in red ink, every stitch allowance marked around the pattern piece, and each piece is thoroughly labeled (which product it is, what piece it is of that product, dimensions, date created, etc.) Separate pattern pieces are made for each product including trim allowance (to get a nice edge after stitching) and the final size of the product as well to check my work in the trimming and assembly stages. These pattern sheets are used to trace onto leather using a scratch awl.
-
As far as the crafting of each piece, it is hard to describe an order-of-operations because each design requires a different set of steps. A basic overview is that the pieces are cut, stamped with the Mooney Leather Goods logo, glued, chiseled and stitched, trimmed to get a crisp edge, sanded, and finally burnished. More often than not, some burnishing or stitching must be done before assembly because it will not be accessible later.
-
The final step is examining each piece closely. I check the stitch lines, the edge finishing, and every surface for imperfections. It is handmade, and the leather will have natural imperfections, but I want every item to be durable, functional, and to look good. Each pocket is opened up a little bit with a bone folder, a card is inserted to check the fit of wallet pockets, and each piece is oiled.